Dificultades en la preparación de los recubrimientos térmicos con spray
Cómo estimar la porosidad real en un revestimiento pulverizado y preparado metalográficamente sigue siendo un tema de discusión, ya que el esmerilado y el pulido metalográficos, si no se realizan correctamente, pueden introducir artefactos que no formen parte de la estructura de revestimiento.
Por ejemplo, en revestimientos metálicos o cerámicos/metálicos, el metal más blando se arrastra a los poros durante el esmerilado y, si no se pule adecuadamente, puede tapar la verdadera porosidad. En comparación, los revestimientos cerámicos son quebradizos y, durante el esmerilado, se desprenden partículas de su superficie. Si no se pulen correctamente, estas partículas desprendidas podrán malinterpretar una porosidad alta.
En general, las dificultades comunes con la preparación de recubrimientos térmicos con spray en el proceso metalográfico incluyen:
Corte: La sujeción de piezas recubiertas durante el proceso de corte puede introducir fracturas en los revestimientos más frágiles o comprimir los que son muy blandos.
Embutición: Las resinas de embutición en frío con una contracción alta pueden ocasionar daños en los revestimientos con una adhesión débil al substrato; debido a la hendidura de contracción el revestimiento carece del soporte de la resina, lo que puede producir una delaminación del revestimiento durante el esmerilado y pulido.
Esmerilado y pulido: El redondeo de bordes puede generar un pulido irregular y una malinterpretación posterior de la densidad del recubrimiento. Además, el relieve entre el recubrimiento y el substrato crea una sombra que se puede malinterpretar.
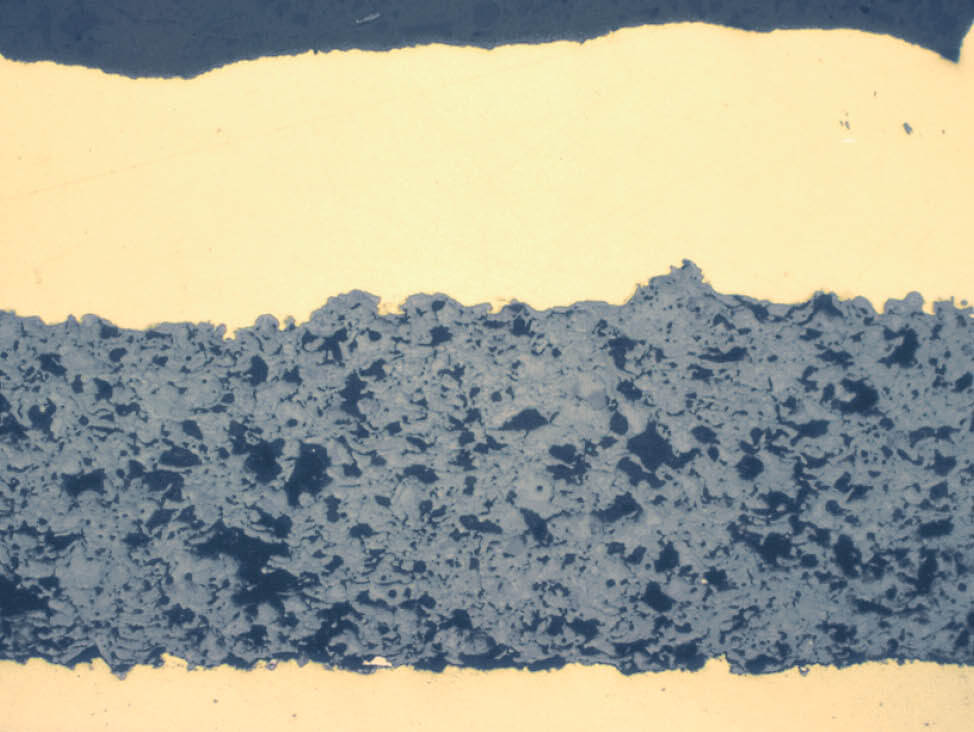
Fig. 1: Recubrimiento cerámico pulverizado, con pulido insuficiente
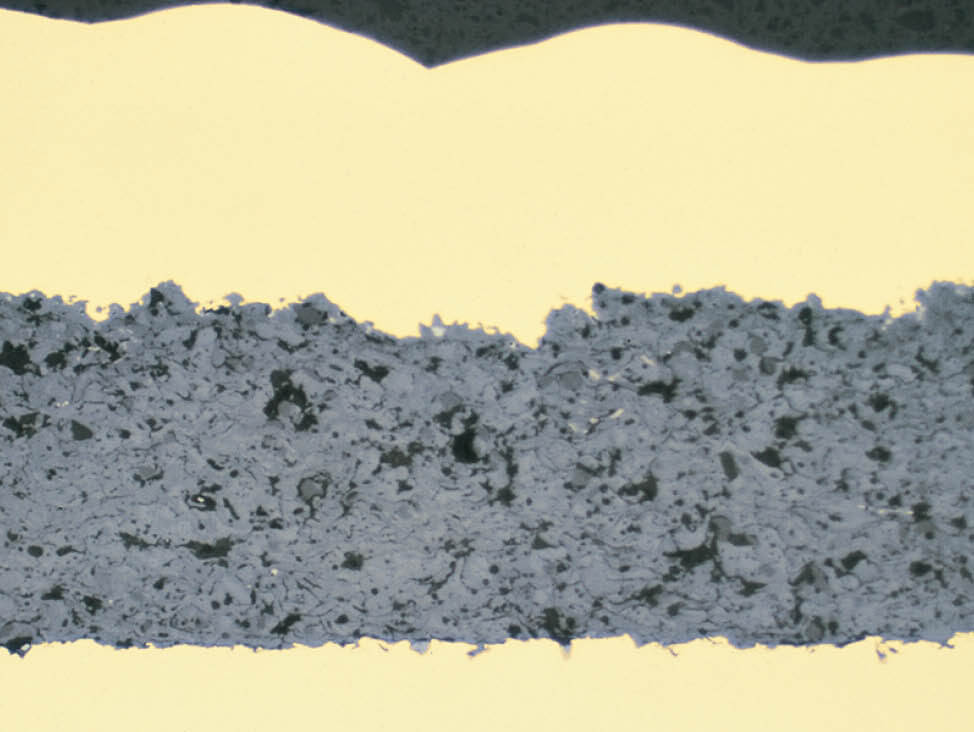
Fig. 2: Mismo recubrimiento que en la Fig. 1, pero pulido correctamente
Fig. 3: El redondeo de bordes puede generar un pulido irregular y una malinterpretación posterior de la densidad del recubrimiento. En ese caso, un pulido incorrecto sugiere menos porosidad en el medio del recubrimiento.

Fig. 4: El relieve entre el recubrimiento y el substrato crea una sombra que se puede malinterpretar. En ese caso, un recubrimiento con spray de carburo sinterizado WC/Co con relieve muestra una línea oscura en interfaz de resina/recubrimiento.