Comprendre les alliages
Les matériaux utilisés dans les applications pratiques aujourd’hui sont un mélange de différents éléments chimiques, souvent appelés « alliages ». L’acier et la fonte, par exemple, sont essentiellement des alliages à base de fer (Fe) et d’additions de carbone (C), qui déterminent la dureté du matériau ferreux. L’analyse microstructurelle nous permet de tirer des conclusions concernant les propriétés de l’alliage, notamment sa résistance, sa dureté et sa ductilité.
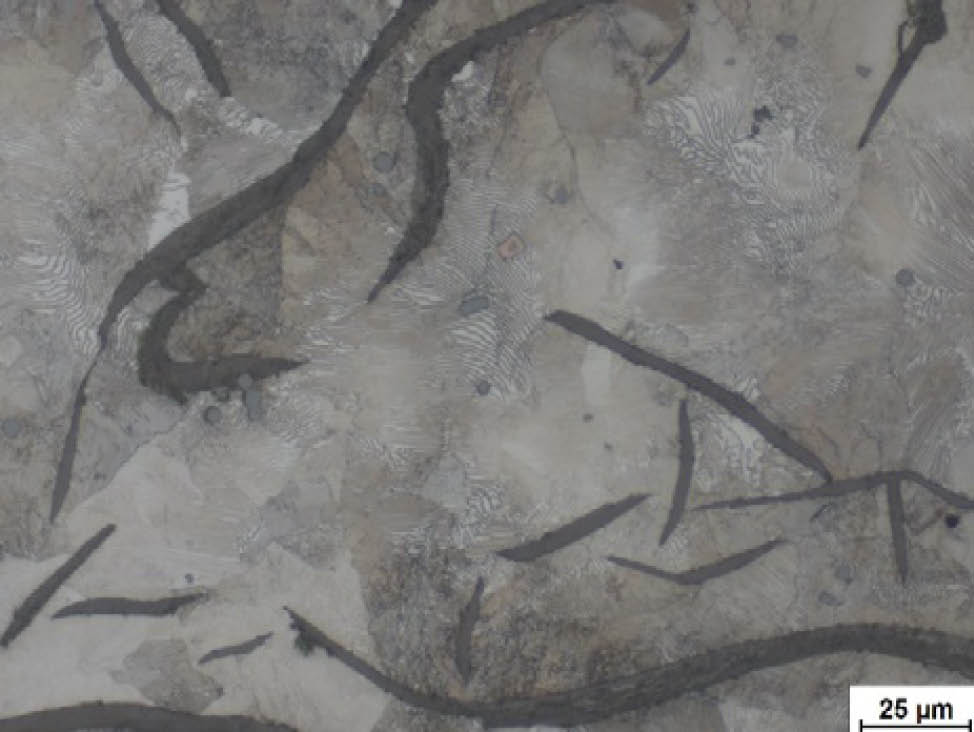
Fig. 3 : fonte perlitique à graphite lamellaire, attaque avec du Nital. Le carbone est principalement présent sous forme de graphite sous forme lamellaire, ce qui se traduit par une résistance réduite. La matrice perlitique elle-même présente un degré de dureté suffisamment élevé.
Image réalisée avec ZEISS Axio Imager, objectif 50x ; éclairage en champ clair
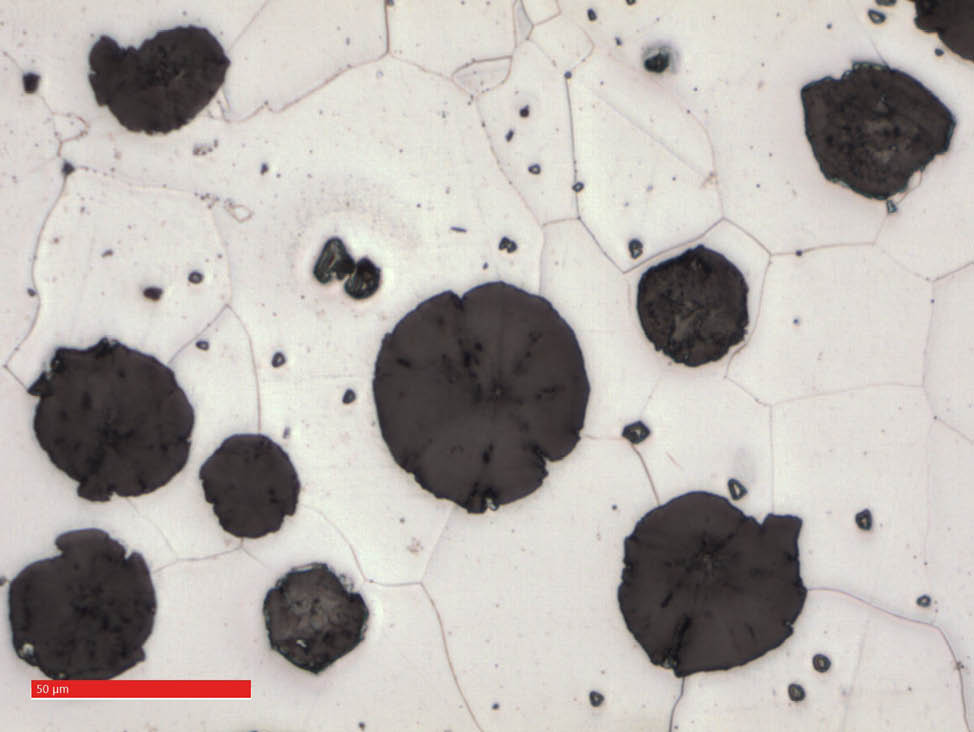
Fig. 4 : fonte ferritique à graphite sphéroïdal, attaque avec du Nital. Le carbone est principalement présent sous forme de graphite sous forme sphérique. La forme sphérique produit une résistance supérieure à celle de la fonte lamellaire ; cependant, la dureté du matériau est moindre, en raison de l’absence de cémentite dans la matrice purement ferritique.
Image réalisée avec ZEISS Smartzoom 5, grossissement d’environ 500x
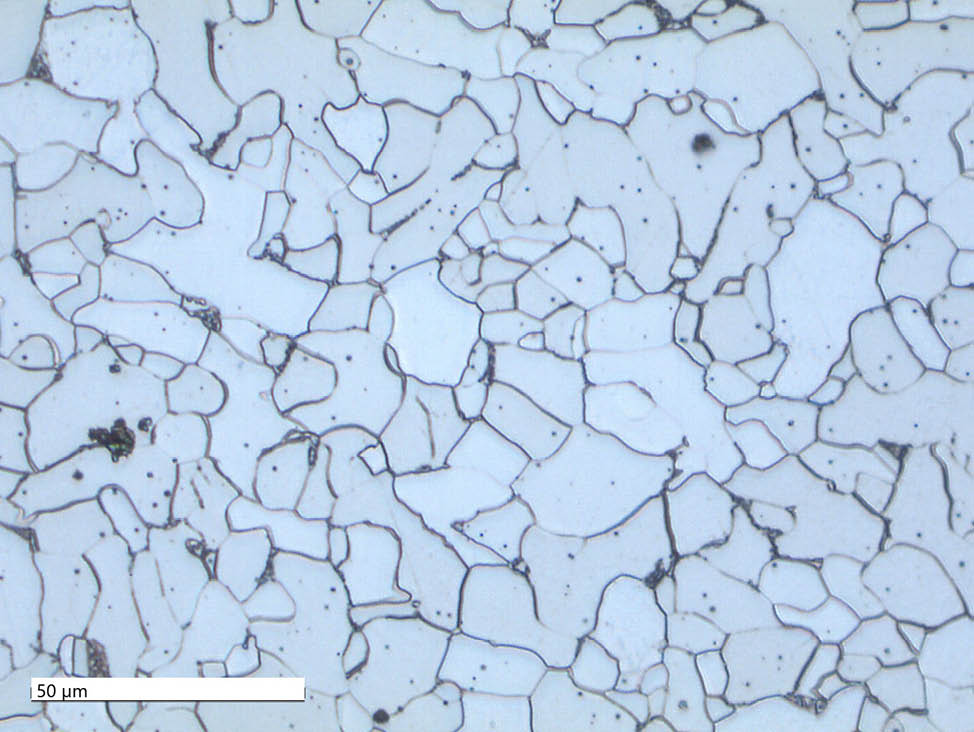
Fig. 5 : acier ferritique avec environ 0,1 % de carbone, attaque avec du Nital. Le carbone est principalement présent sous forme de cémentite et d’une faible proportion de perlite entre les grains ferritiques. La matrice, qui est donc presque purement ferritique, possède une faible dureté, mais une très bonne ductilité.
Image réalisée avec ZEISS Smartzoom 5, grossissement d’environ 500x ; éclairage coaxial avec faible proportion de lumière annulaire
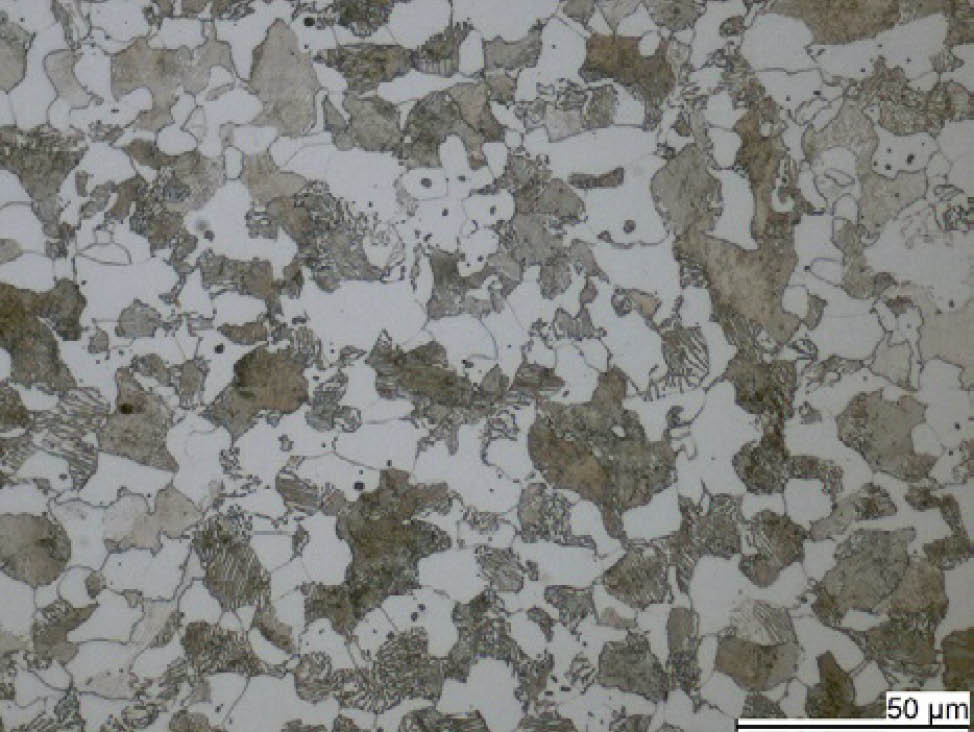
Fig. 6 : acier ferritique-perlitique avec environ 0,2 % de carbone, attaque avec du Nital. Le carbone est principalement présent sous forme de cémentite lamellaire et d’une proportion supérieure de perlite adjacente aux grains ferritiques. Ceci confère à la cémentite une apparence striée. Les grains perlitiques réfléchissent moins la lumière que les grains ferritiques, et ont donc une apparence plus foncée. Une matrice de ce type possède une dureté plus élevée, mais une ductilité plus faible.
Image réalisée avec ZEISS Axiolab, objectif 50x ; éclairage en champ clair