Understanding alloys
The materials used in practical applications today are a mixture of various chemical elements, often also referred to as ‘alloys’. Steel and cast iron, for example, are essentially alloys based on iron (Fe) with carbon (C) alloying additions, which are responsible for the hardness of the ferrous material. Microstructural analysis enables us to draw conclusions regarding the properties of the alloy, including its strength, hardness and ductility
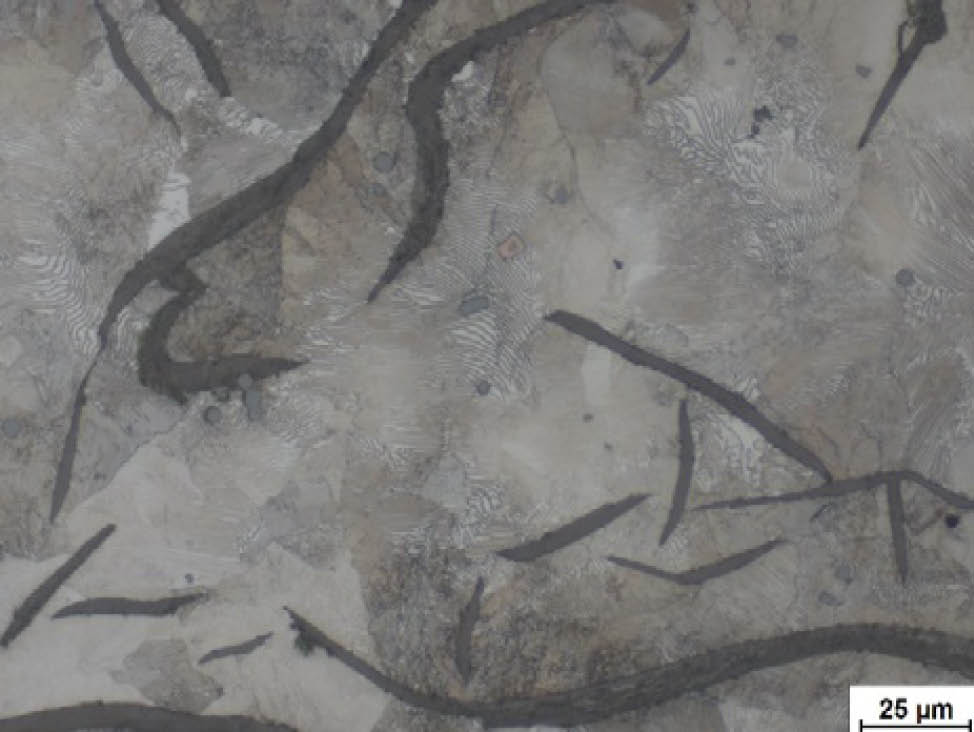
Fig. 3: Pearlitic cast iron with lamellar graphite, etched with Nital. The carbon is primarily present as graphite in a lamellar form, which results in reduced strength. The pearlitic matrix itself exhibits a sufficiently high degree of hardness.
Image taken with ZEISS Axio Imager, 50x objective, brightfield illumination
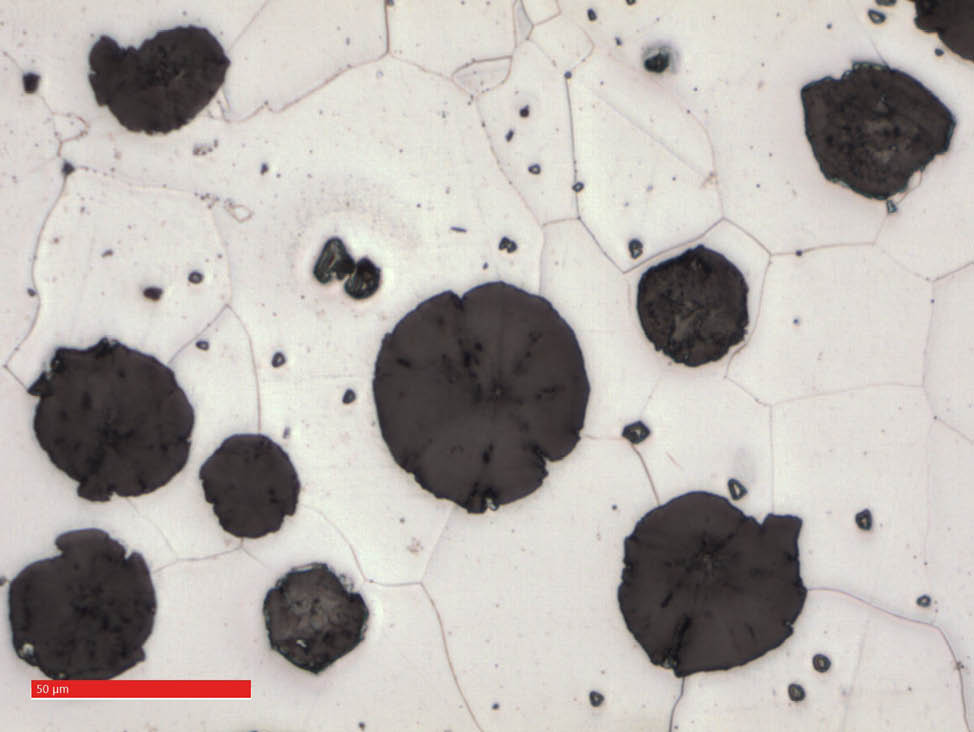
Fig. 4: Ferritic cast iron with spheroidal graphite, etched with Nital. The carbon is primarily present as graphite in a spherical form. The spherical form results in improved strength in comparison to lamellar cast iron, but the hardness of the material is lower due to the lack of cementite in the purely ferritic matrix.
Image taken with ZEISS Smartzoom 5, at approx. 500x magnification
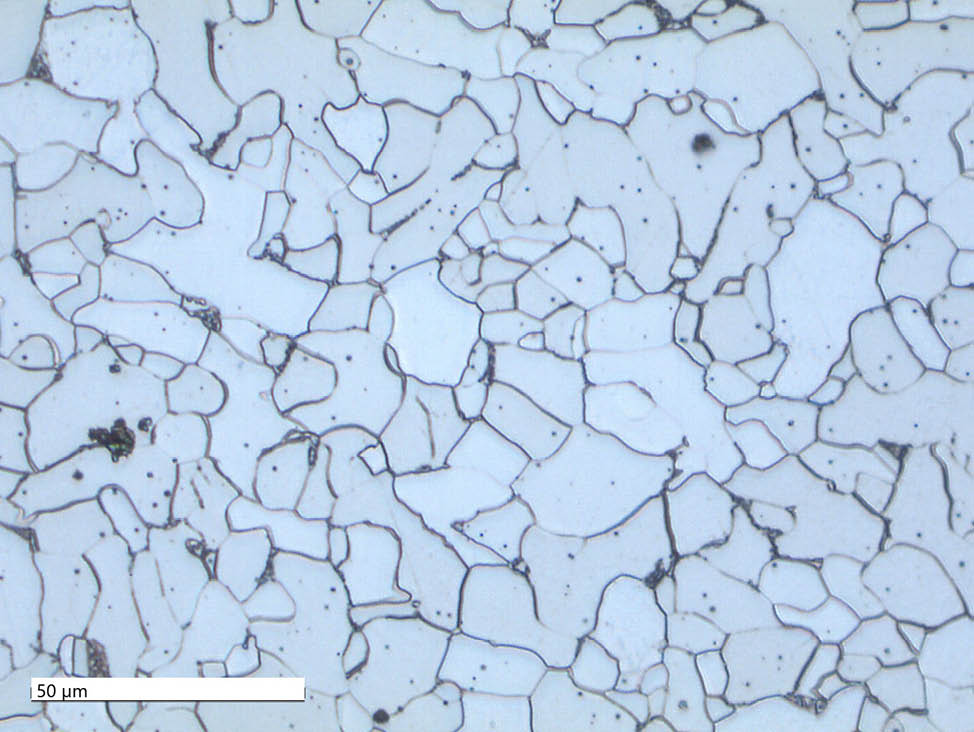
Fig. 5: Ferritic steel with approx. 0.1 % C, etched with Nital. The carbon is primarily present in the form of cementite and as a low proportion of pearlite between the ferritic grains. The matrix, which is therefore nearly purely ferritic, has a low degree of hardness but very good ductility.
Image taken with ZEISS Smartzoom 5 at approx. 500x magnification, coaxial illumination with low proportion of ring light
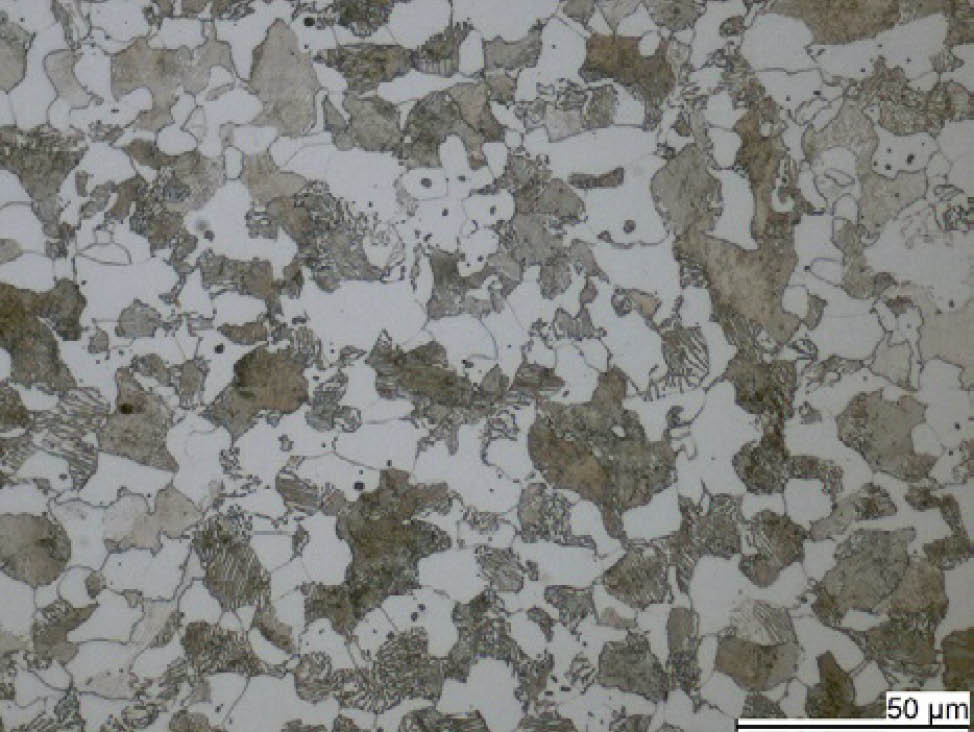
Fig. 6: Ferritic-pearlitic steel with approx. 0.2 % C, etched with Nital. The carbon is primarily present as a cementite lamellar in a harder proportion of pearlite adjacent to the ferritic grains. This causes the cementite to appear streaky. The pearlitic grains reflect less light than the ferritic grains and thus appear darker. A matrix of this type has higher hardness, but lower ductility.
Image taken with ZEISS Axiolab, 50x objective, brightfield illumination