Fastener production and fastener technology
Simple non-threaded metal fasteners, such as pins and rods, are one of the oldest fastener technologies. Threaded rivets, screws and bolts came later and were first made from precious metals.
One of the biggest developments in fastener technology came with the arrival of ductile metals that could withstand the pressure of pressing and rolling. At this point, cold forming was adopted for the mass production of metal fasteners. Today, chipless shaping (rolling) is widely used, with forming either through cold or hot pressing.
Cold forming of metal fasteners
Cold pressing is by far the most common method for producing metal fasteners. A continuous wire is fed into an extrusion press. A die is then used to compress the wire and reduce its diameter, until the correct shape is formed. The threads are formed by cold rolling. In some cases, induction hardening may be used to increase the surface hardness of the metal fastener.
- For high-quality steel fasteners, various heat treatments are used to achieve specific material properties.
- Low-carbon steels are carburized to create a hard surface with a soft and ductile center.
- Carbon steels are hardened and tempered.
- Very high-quality construction screws may be machined after initial shaping to achieve specific shapes, tolerances and surfaces.
Hot forming of metal fasteners
Hot forming may still be used for very large or complex-shaped metal bolts.
Corrosion protection of metal fasteners
For improved corrosion protection, fasteners may be coated with manganese, zinc or iron phosphate and then oiled. If greater corrosion protection is required, metal fasteners can be galvanized with zinc and cadmium or chromium plating, or vapor deposition coated with cadmium and aluminum.
Find out more
To get a detailed description of the various processes and technologies involved in the production of metal fasteners,
download the full application note.
Fig. 3: Cold heading is a basic operation in which the round wire stock is formed into the necessary shape while still "cold". The operation must retain continuity of grain to assure the full integrity of the metal fastener.
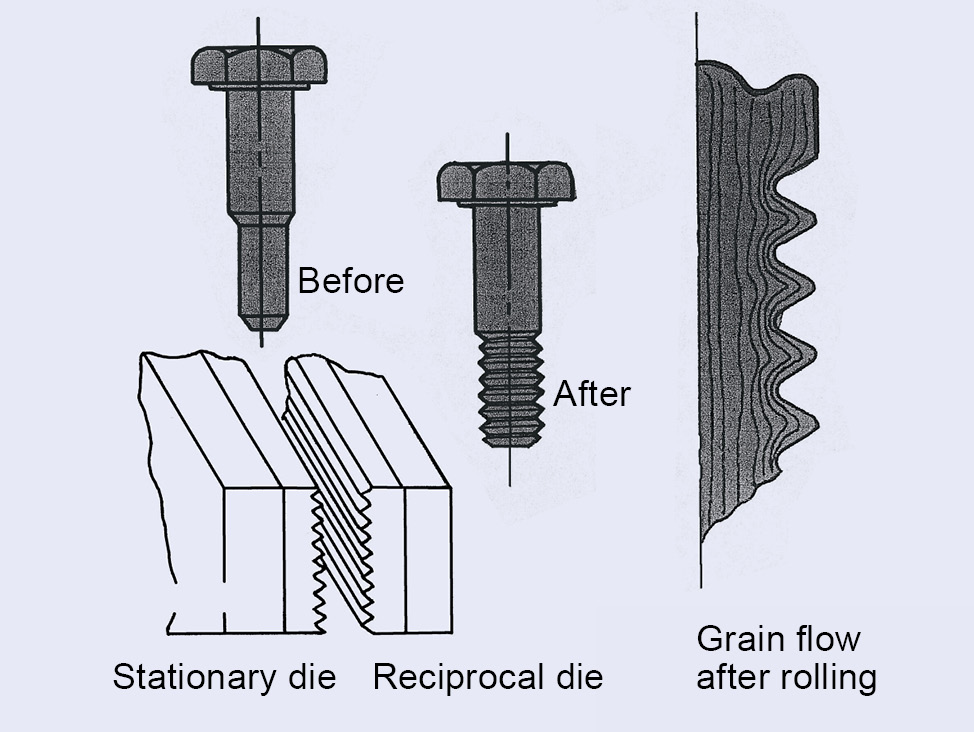
Fig. 4: In thread rolling, a blank is rolled between two flat dies with precise parallel grooves. A cold or warm operation, rolled threads are strong and smooth, and no material is wasted.