Grinding, polishing & etching of additive manufactured parts
When working with additive manufactured specimens, the grinding, polishing and etching stages of preparation vary greatly, depending on the material/alloy. Here are brief recommendations for four common materials used in AM.
Titanium
In general, preparation should follow the standard methods used for other titanium specimens.
- Due to its high ductility, titanium is prone to mechanical deformation and scratching. Diamond polishing should be avoided, especially with pure titanium.
- For less alloyed titanium, electropolishing is recommended.
- To reveal more information, etching is often required after mechanical or electrolytic preparation. As titanium is chemically resistant, etchants containing hydrofluoric acid are recommended.
- Polarized light is an excellent optical etching method for titanium.
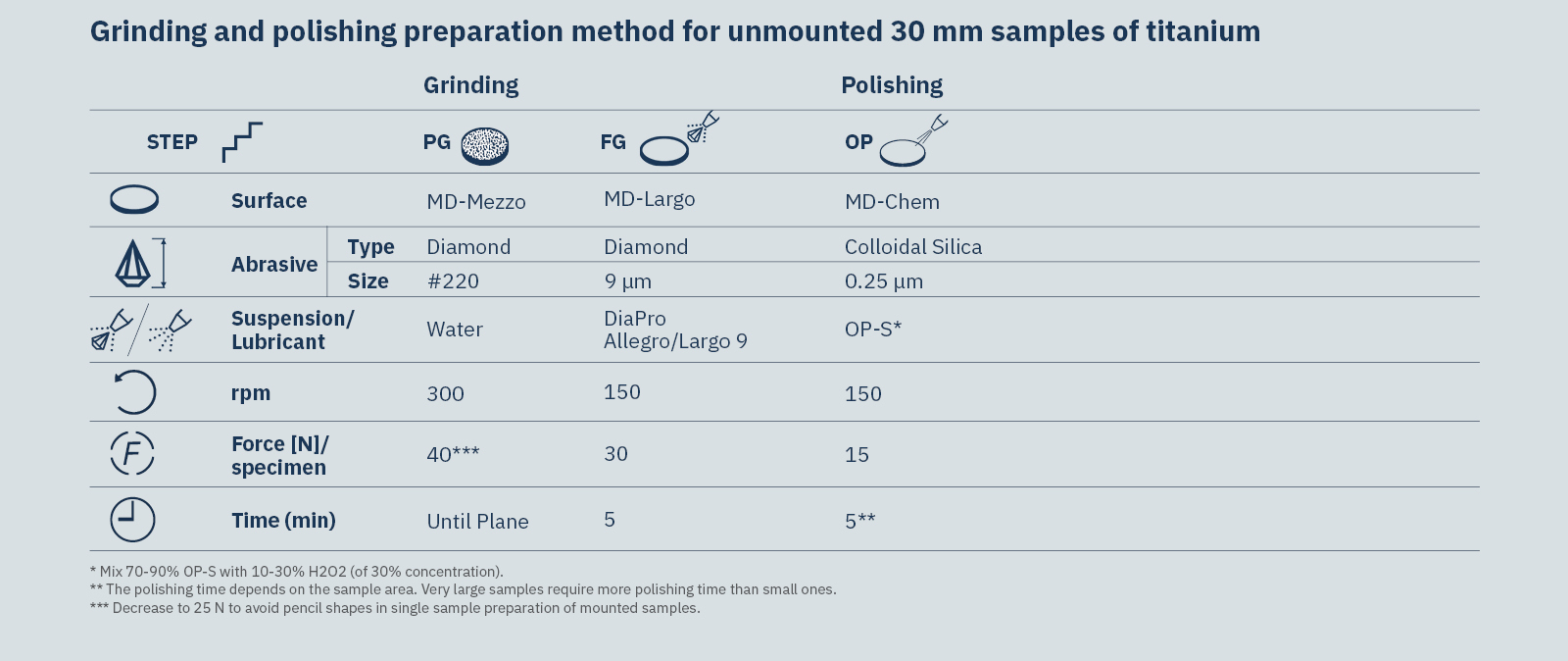
Table 2. Grinding & polishing preparation method for unmounted 30 mm samples of titanium.
See the full application note for detailed descriptions and proven methods for polishing, electropolishing and etching of titanium additive manufactured specimens.
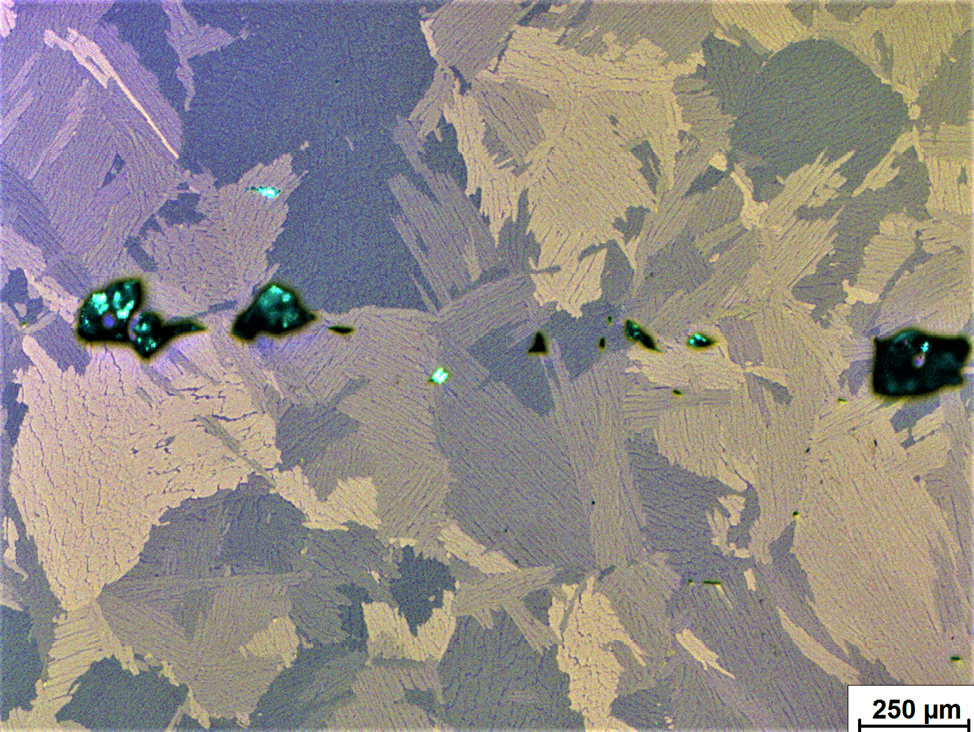
Figure 14. Final polished titanium specimen with pores. Polished on MD-Chem with OP-S NonDry and additive, with a visible microstructure in polarization contrast.
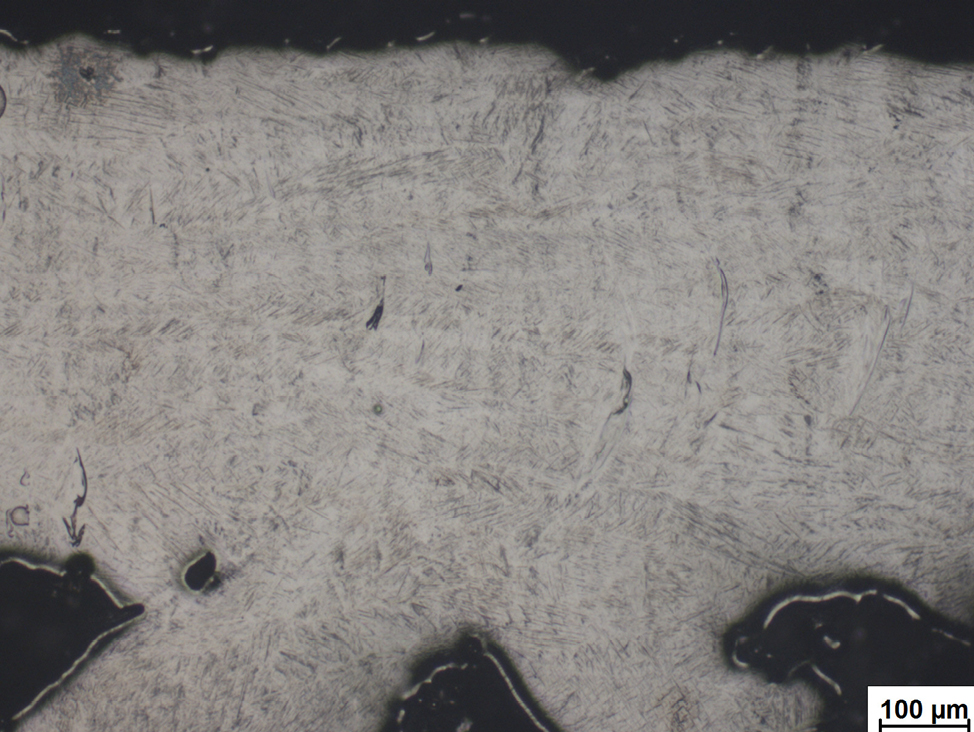
Figure 15. Titanium alloy. Electrolytical preparation with A3, not mounted. Bright field.
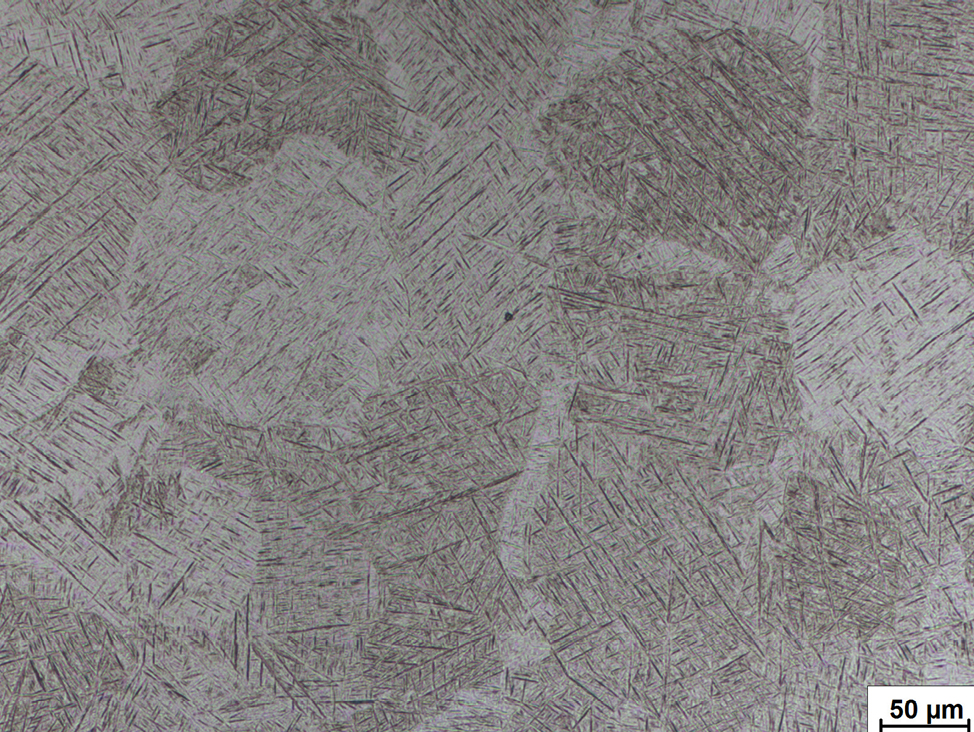
Figure 16. Titanium alloy. Electrolytically polished and chemical etched with Fuss etchant. Bright field.
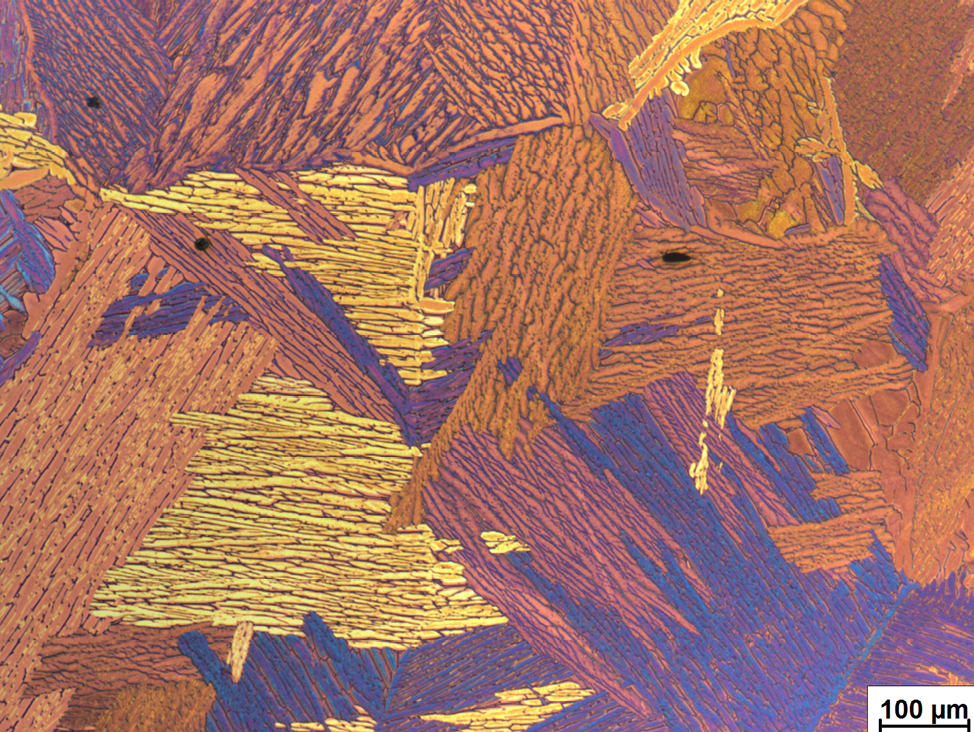
Figure 17. Titanium alloy after etching with Keller etchant. Polarized light.
Aluminum
Although aluminum is soft, alloying elements can significantly change its mechanical properties. In general, preparation of additive manufactured specimens should follow the methods used for similar aluminum specimens.
- To avoid deformation, scratching and edge rounding, it is recommended to use a rigid plane grinding surface specifically developed for aluminum alloys, called MD-Molto.
- When fine grinding, MD-Largo with diamond suspension (e.g., DiaPro Allegro/Largo) is suitable for many types of aluminum.
- To ensure thorough polishing, follow the fine grinding with a diamond polishing (MD-Mol) and an oxide polishing (colloidal silica, OP-U) steps.
- To reveal more or specific details, chemical, electrolytical, and optical etching methods, or a combination, can be used.
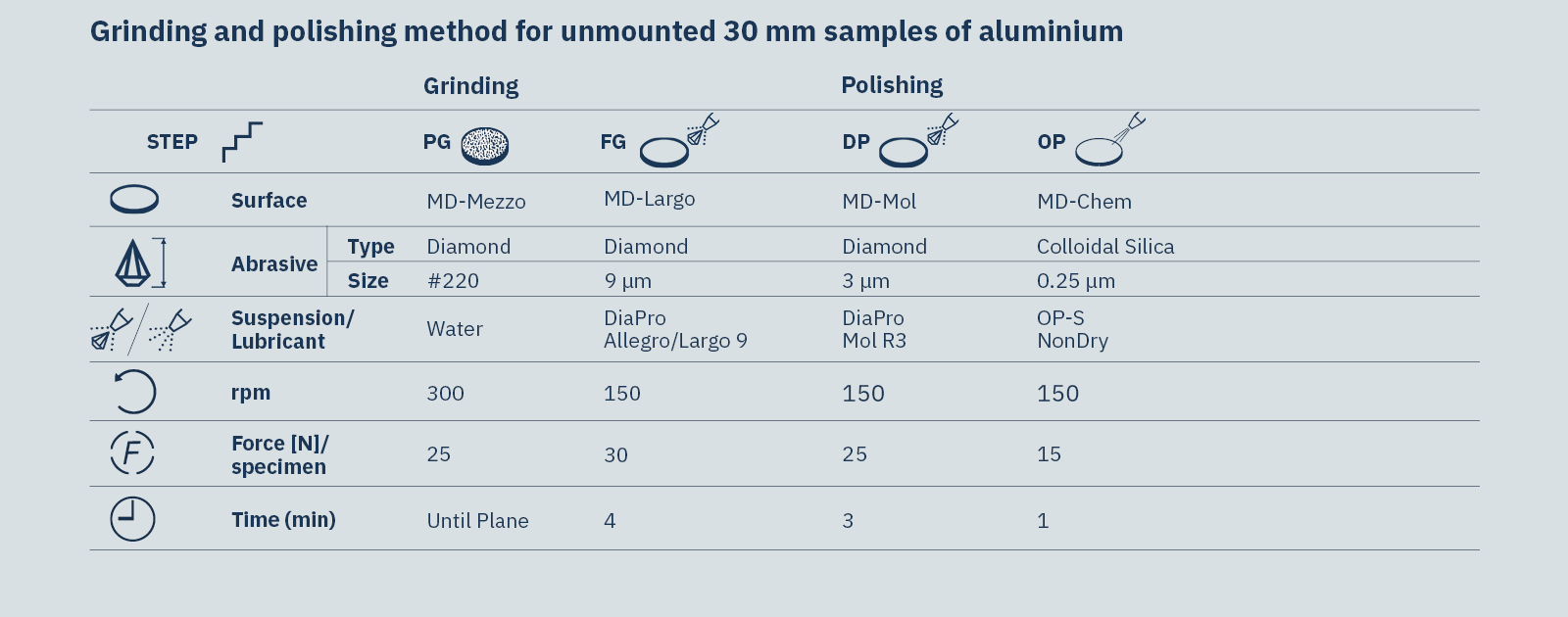
Table 3. Grinding & polishing method for unmounted 30 mm samples of Aluminium
For more detailed information and methodology, see the full application note.
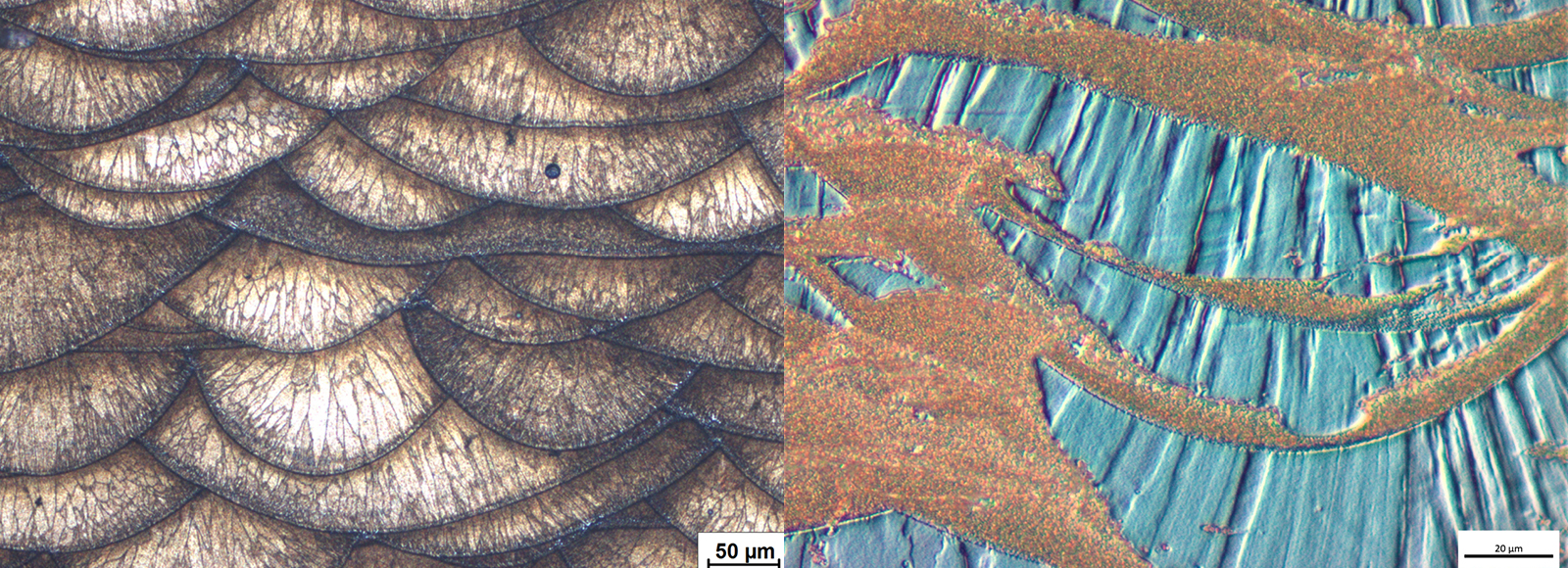
Figure 18. Different aluminium alloys after Barker‘s etching in bright field (left) and in differential interference contrast, DIC, (right).
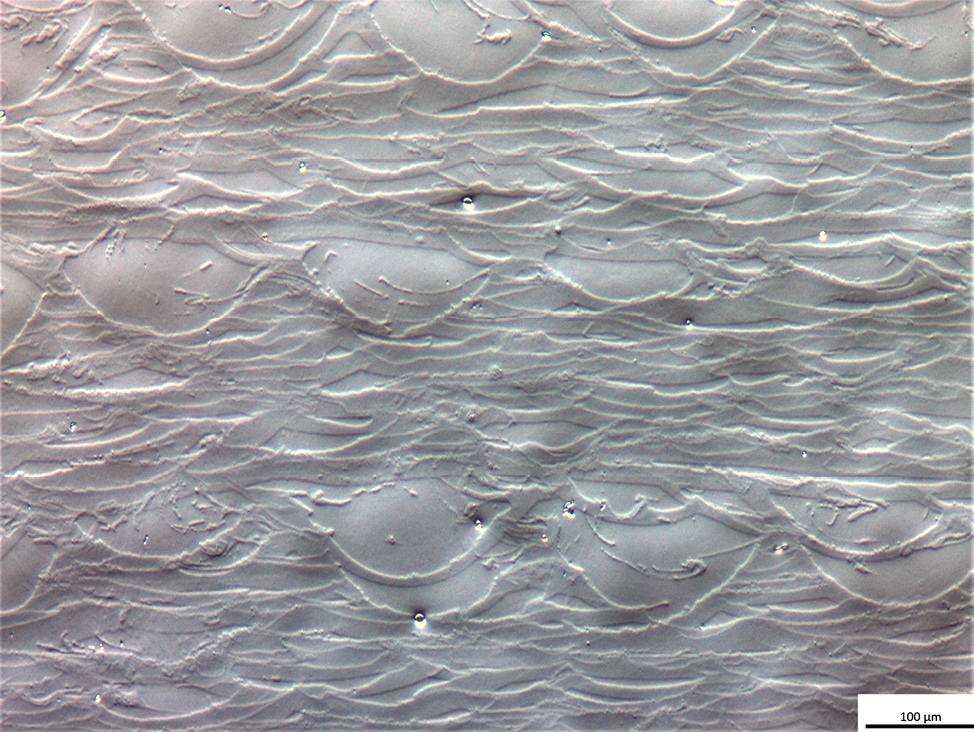
Figure 19. Fine polished surface of aluminium alloy. Polished with MD-Chem and OP-S. Differential interference contrast, DIC, unetched.

Figure 21. Overview of aluminium alloy, etched with Barker’s (left). Detail of aluminium alloy, with precipitation in high magnification (right). Bright field.

Figure 22. Aluminium alloy after Barker’s etching (left). Inconel etched with Adler (right). Polarized light.
Stainless steels and nickel-based alloys
As these materials are often soft and ductile, very coarse grinding surfaces and high pressure should be avoided. In general, the preparation should follow the standard methods used for other stainless steels and nickel-based alloys.
- Use a dedicated plane grinding disc, such as MD-Alto.
- Fine grinding should be carried out with diamond suspension on a rigid disc (MD-Largo) or MD-Plan cloth.
- Follow fine grinding with a thorough diamond polish on a medium/hard cloth (MD-Dac).
- We recommend a final polish with colloidal silica (OP-S) or alumina (OP-A) to remove any fine scratches.
- Electrolytic etching with 10 % oxalic acid in water is common. However, for duplex steels, electrolytic etching with NaOH (20 % in water) delivers better results.
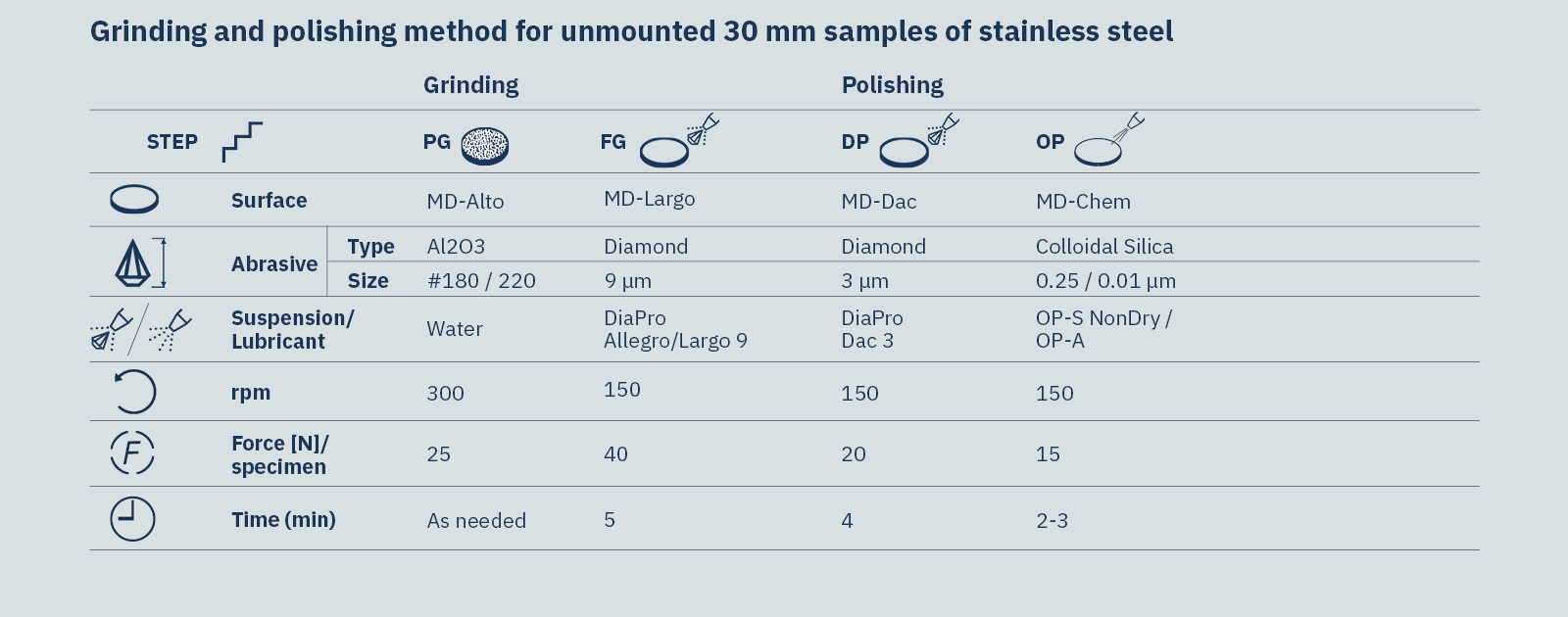
Table 4. Grinding & polishing method for unmounted 30 mm samples of Stainless Steel
For more detailed information and methodology, including how to prepare specimens for porosity evaluation, see the full application note.

Figure 24. Austenitic steel after polishing with OP-S on MD-Chem. Structure visible without chemical etching. Differential interference contrast, DIC.
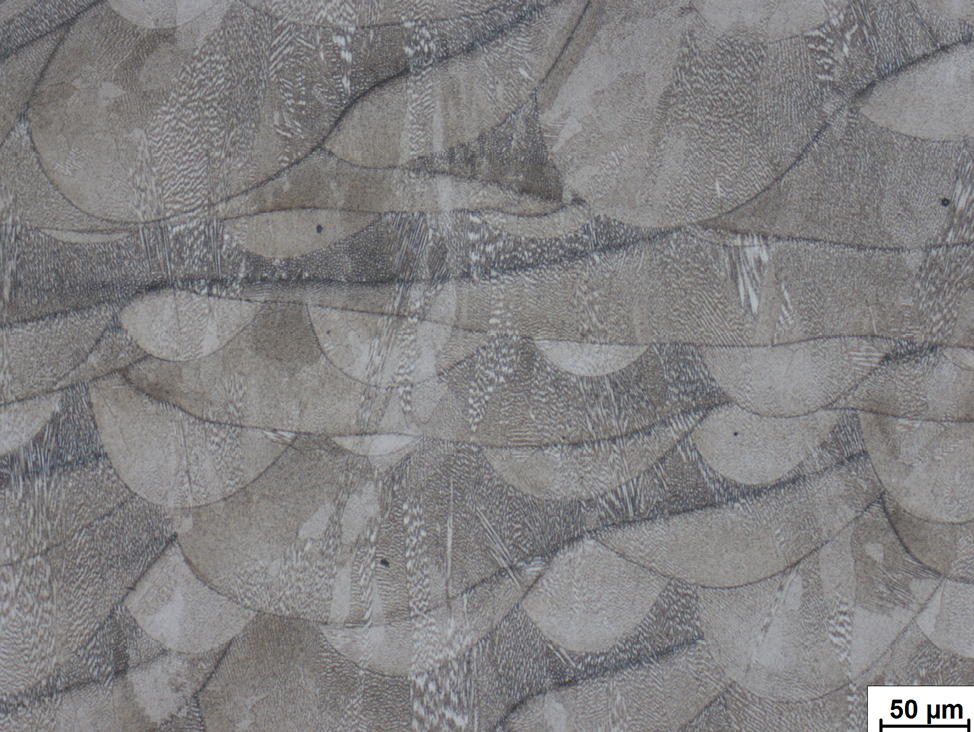
Figure 25. Inconel 718, etched with Adler etchant. Bright field.
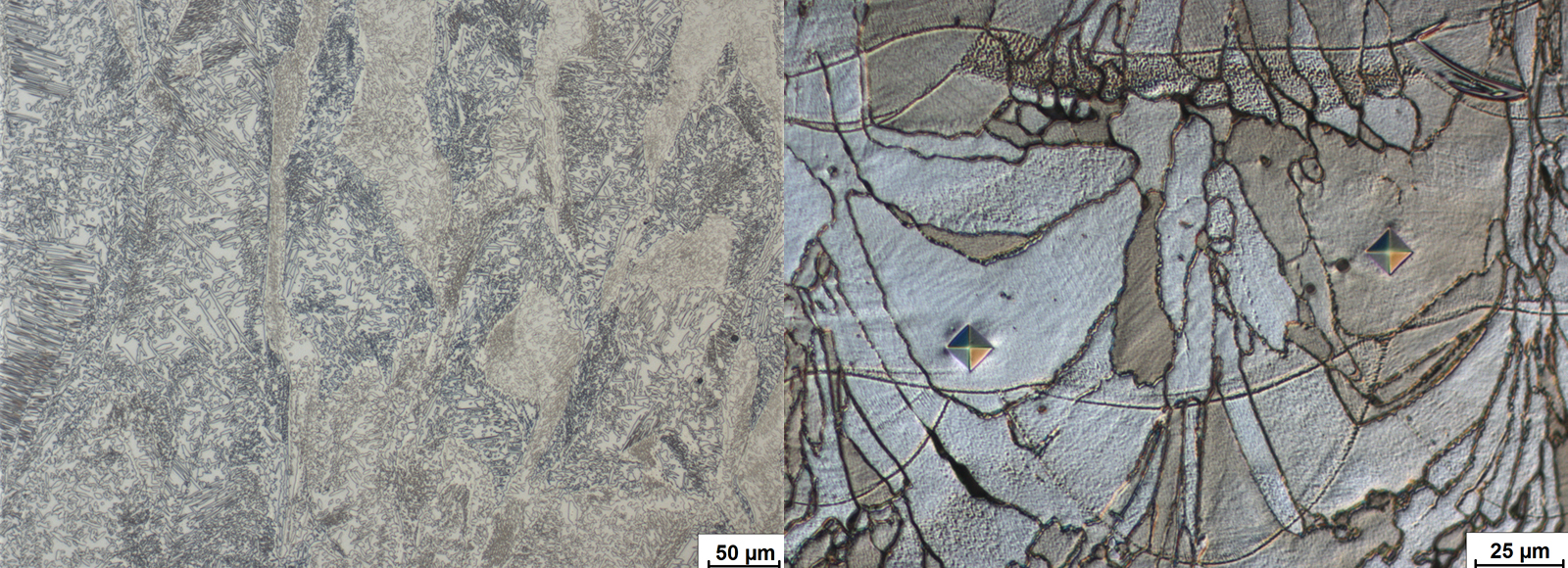
Figure 26. Duplex steel 1.4462 after electrolytic etching with oxalic acid (10%). Bright field (left). Duplex steel 1.4410 with micro hardness indents, after electrolytical etching with 20 % NaOH in water. Differential interference contrast, DIC (right).
Tool steels
Tool steel is made with large amounts of alloying elements, such as chromium, nickel, vanadium, or molybdenum. The main challenge when grinding and polishing is ensuring that carbides and non-metallic inclusions are retained. In general, preparation should follow the standard methods used for other tool steels.
- For plane grinding, it is recommended to use plane grinding discs with embedded diamonds (MD-Piano).
- For fine grinding, use a metal bonded diamond disc (MD-Allegro) with diamond suspension.
- For highly alloyed steels, it is possible to use Klemm etchant.
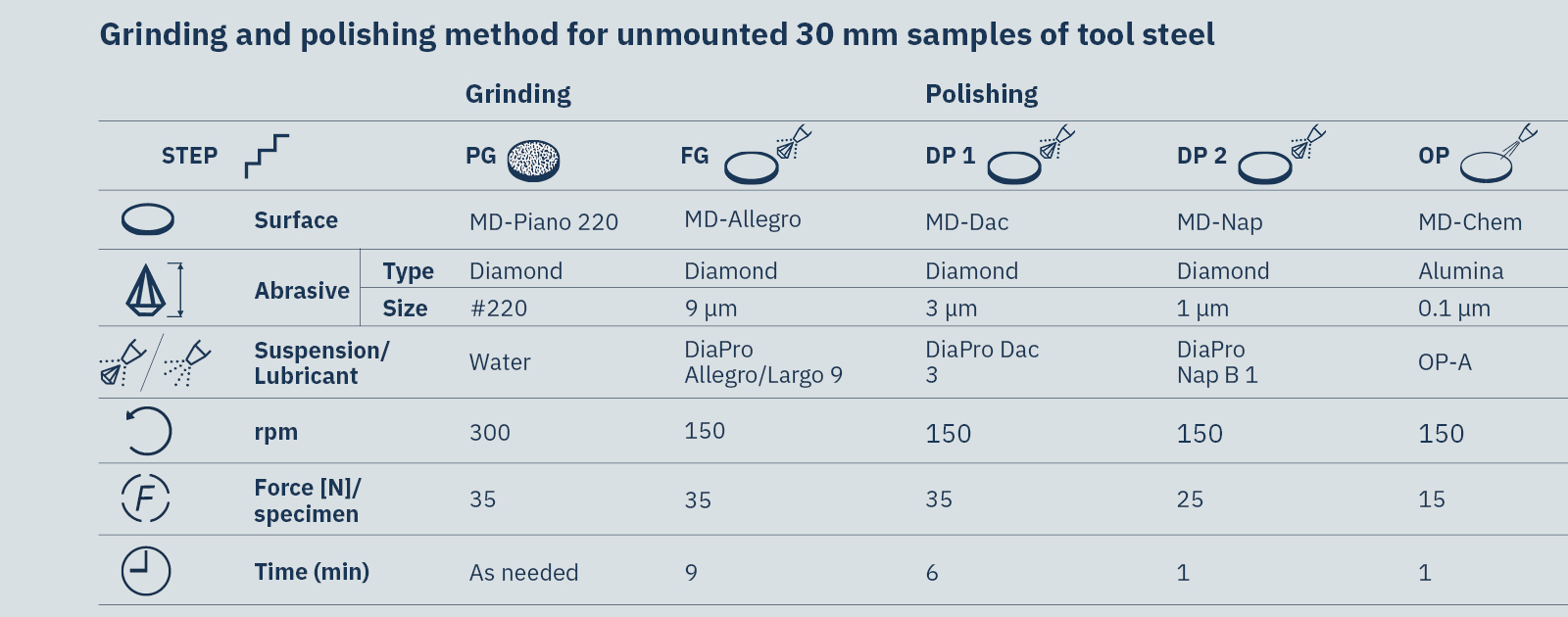
Table 5. Grinding & polishing method for unmounted 30 mm samples of tool steel
See the full application note for more detailed information and methodology.
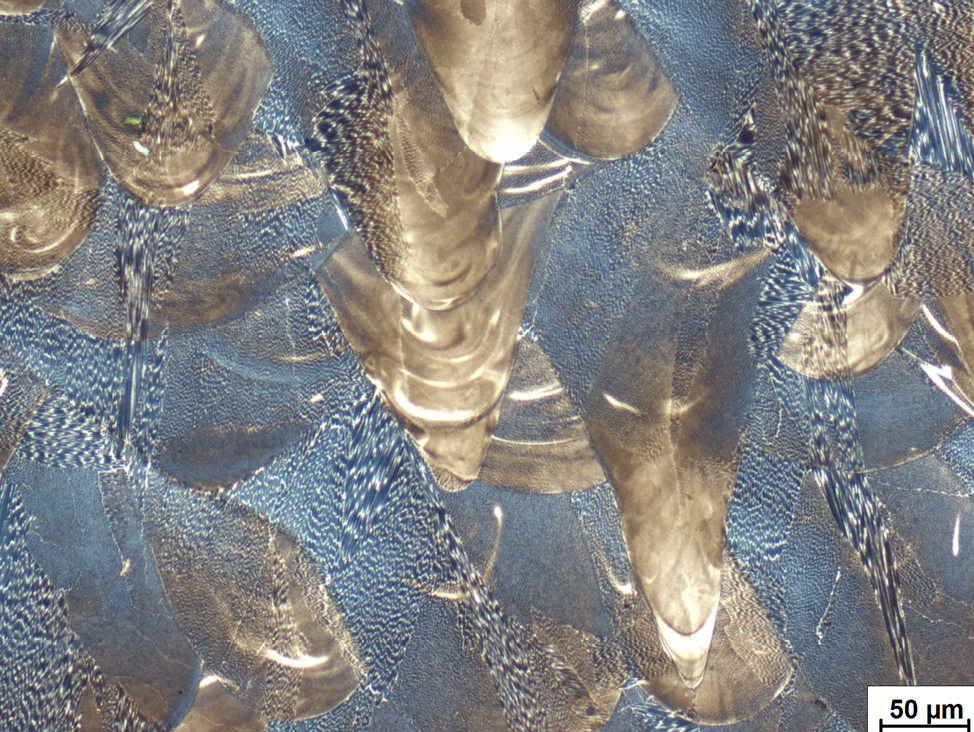
Figure 27. Tool steel 1.2709 after etching with modified Klemm (10/3) and addition of HCl.
Find out more