Preparation of aluminum and its alloys: Mechanical grinding & diamond polishing
When working with aluminum and its alloys, we recommend mechanical grinding, followed by
diamond polishing. For many pure aluminum and wrought alloy specimens, electrolytical polishing is also recommended.
Mechanical grinding
Plane grinding should be carried out with the finest possible grit to avoid excessive mechanical deformation.
- The hardness, size and number of specimens should be considered. However, even with large specimens of pure aluminum, plane grinding with 500# SiC Foil or Paper is usually sufficient.
- Large cast parts of aluminum alloys can be ground with 220# SiC or 320# SiC Foil. It is important that the grinding force is low to avoid deep deformation and to reduce friction between the grinding SiC Foil or Paper and specimen’s surface.
Diamond polishing
Diamond polishing should be carried out until all deep scratches from grinding have been removed. If water soluble constituents must be identified, we recommend polishing with water-free diamond suspension and lubricant.
Final polish for pure aluminum and aluminum alloys: The polish/check sequence
- Begin polishing. After 1 minute of polishing with OP-U suspension, check the specimen under the microscope.
- If necessary, continue polishing for another minute and check the specimen again.
- Continue this polish/check sequence until the required quality has been achieved.
- If diamond particles have been pressed into the surface during polishing, they can lead to erroneous interpretations of the structure. Therefore, the polish/check sequence may need to be relatively long. Continue the sequence until you can no longer see bright and dull areas on the surface of the specimen with the naked eye.
- Approximately 30 seconds before the end of polishing, pour water onto the polishing cloth to rinse the specimen and cloth.
- Finally, wash the specimen again with clean water and then dry it.
Note: Polishing for too long with silicon dioxide suspension OP-S NonDry can cause a pronounced relief, see Fig.11.
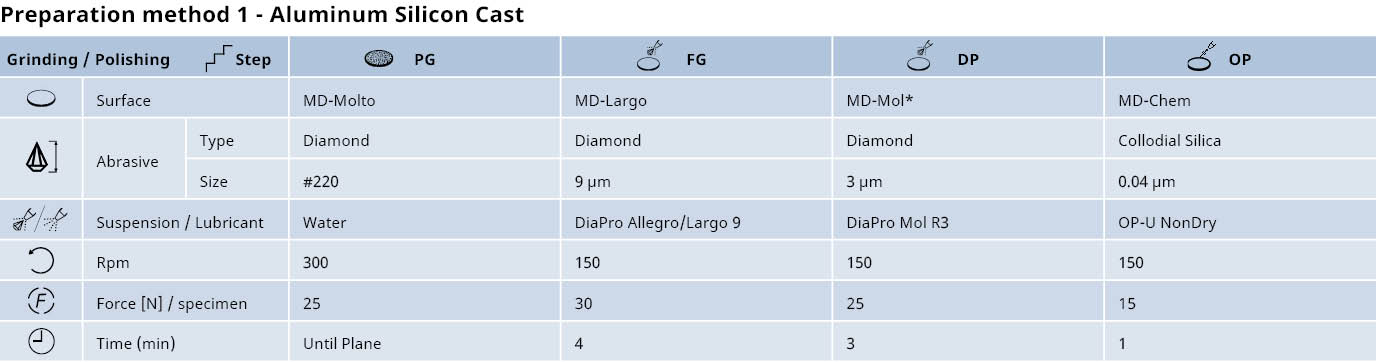
*Alternatively, MD-Dac
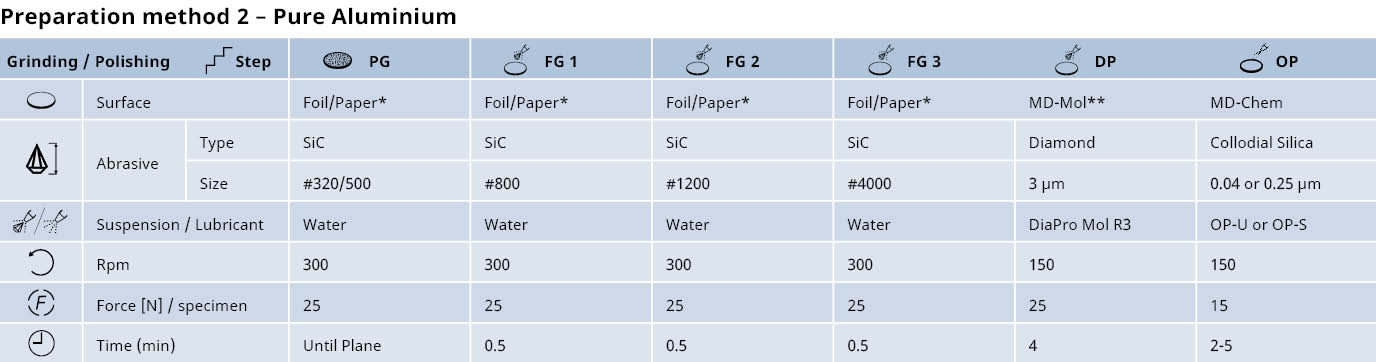
* To avoid coarse scratches, the SiC Foil or Paper can be rubbed with wax before grinding.
** Alternatively, MD-Dac

* To avoid coarse scratches, the SiC Foil or Paper can be rubbed with wax before grinding.'
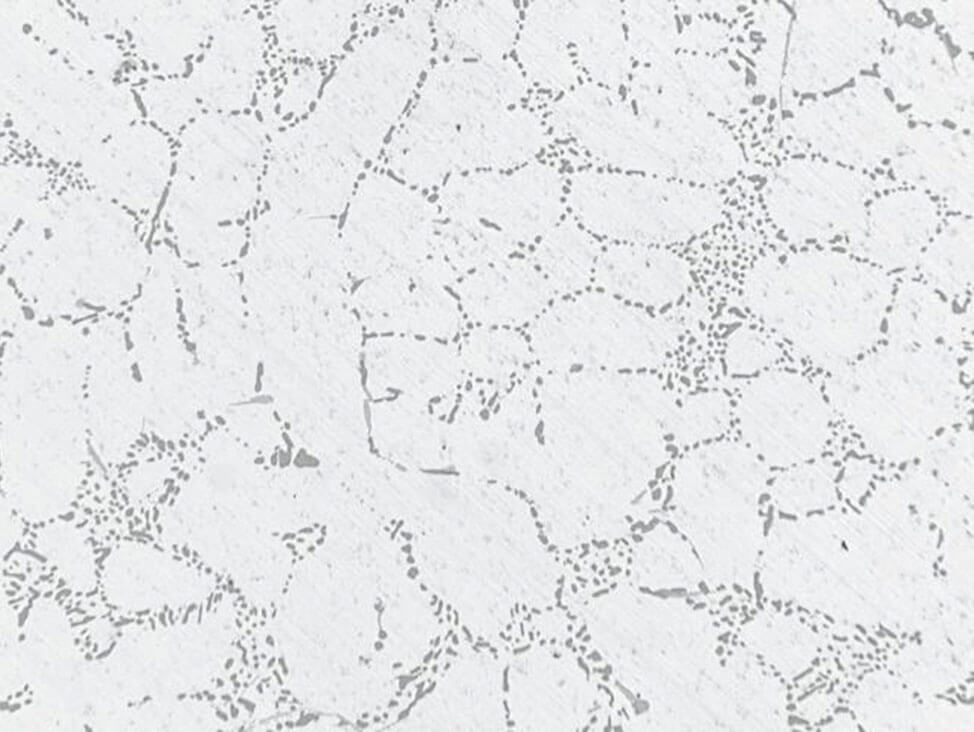
Fig. 9: Aluminum-silicon cast, after polishing with 3 μm diamond small scratches are still visible, 200x
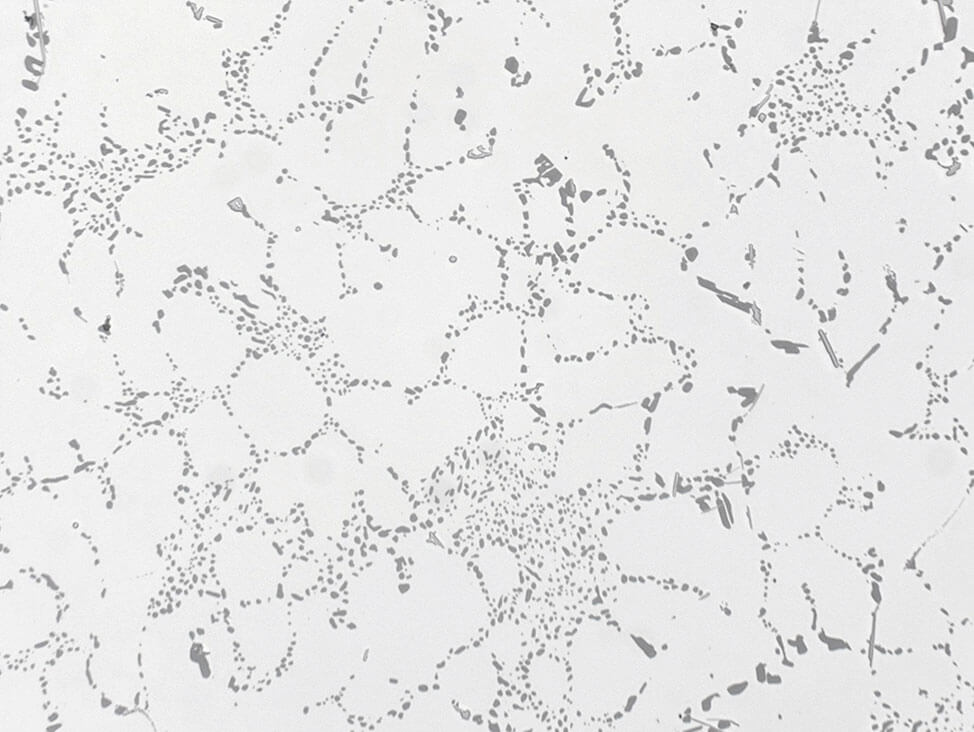
Fig.10: Structure as in Fig. 9, but fine polished with OP-U suspension. The matrix is well polished, and the eutectic has more contrast, 200x
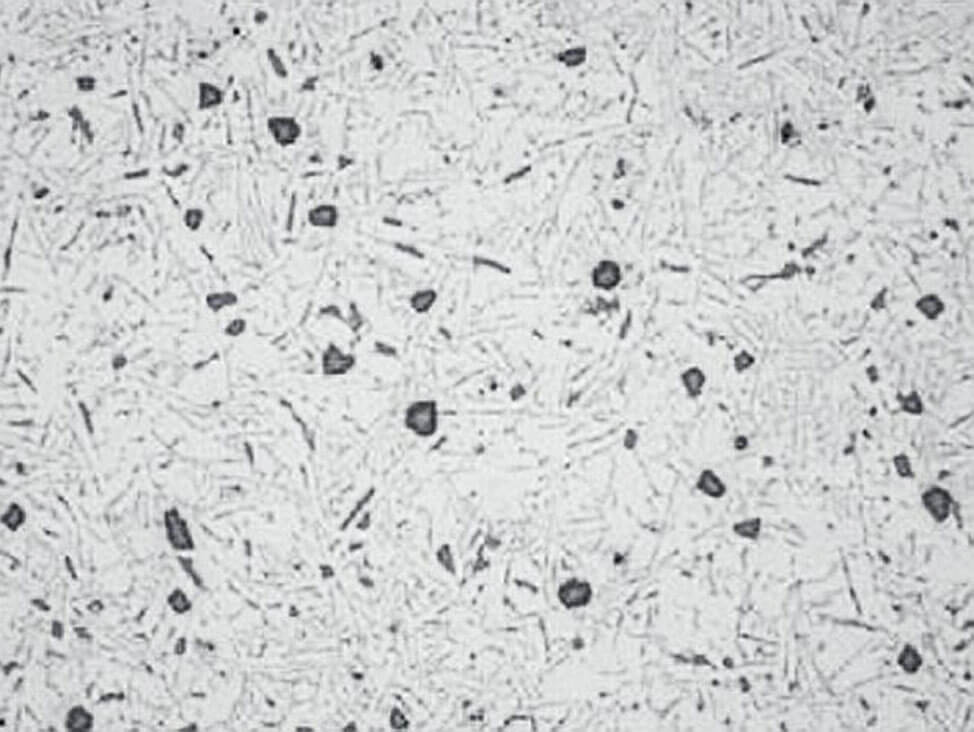
Fig.11: Aluminum-silicon cast polished for too long with OP-S suspension, silicon precipitates stand in relief, 100x
Electrolytic polishing
Electrolytic polishing of aluminum leaves a scratch-free surface and is often used in quality control as it delivers fast and reproducible results. However, it is not recommended for many cast alloy specimens, due to the many different phases in cast alloys.
Pure aluminum and wrought alloys
Electrolytic polishing is especially suitable for pure aluminum and wrought alloys.
- For routine grain size determination at 100x, pre-grinding with 1000# SiC Foil is sufficient.
- Rolled or drawn surfaces do not need any grinding or polishing.
- For pure aluminum and precise examinations of grain shapes, the specimen should be fine ground to 2000# and sometimes even to 4000# before electrolytic polishing.
If you anodize the specimen with Barker’s reagent after the polishing, it will result in a color contrast that is particularly suited for grain size evaluation. To obtain the color effect, view the specimen under polarized light with a λ1⁄4 sensitive tint plate.

Fig.12: Plated sheet, anodized, grain areas are clearly visible and suitable for automatic image analysis, polarized light with λ1⁄4-plate, 100x
Discover the parameters for electrolytic polishing of aluminum in our application note here.
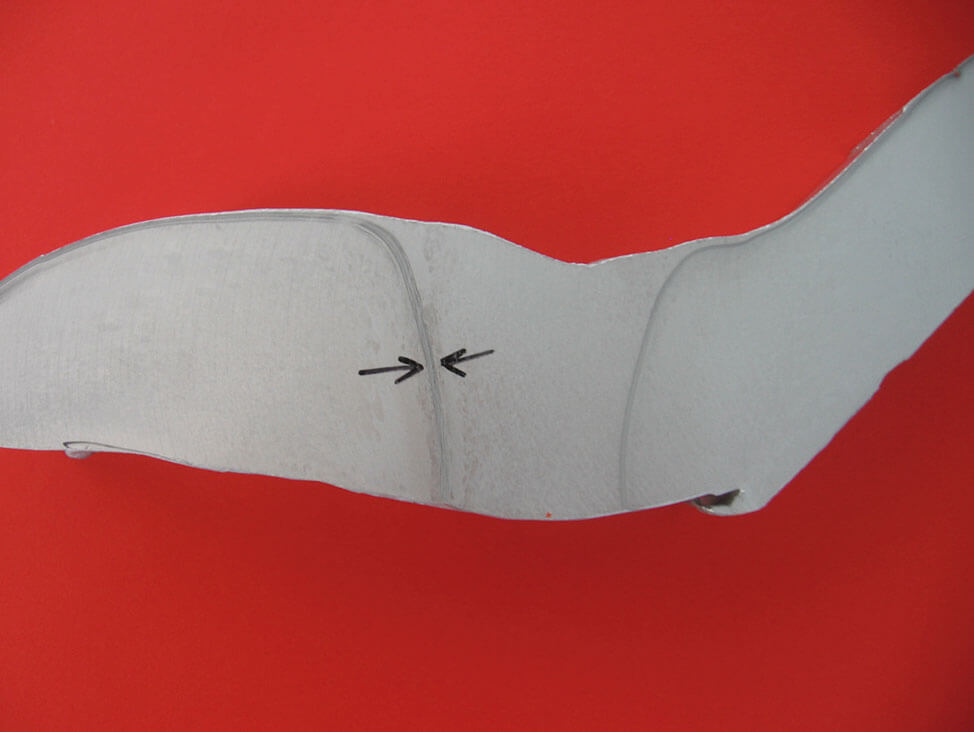
Fig.13: Aluminum pressed part, macro etching, primary and heterogeneous precipitates are revealed